摘要:普光氣田是國內(nèi)目前大規(guī)模開發(fā)的含硫量最高的高酸性氣田,其天然氣具有高壓、高含H2S、含C02的特點。建設處理規(guī)模120×108m3/a的天然氣凈化廠,面臨天然氣凈化難度大、硫磺儲運技術(shù)和安全要求高、生產(chǎn)工藝及安全控制復雜等諸多技術(shù)難題。目前國內(nèi)尚無百億立方米級天然氣凈化以及配套硫磺成型與安全儲運技術(shù)。為此,在優(yōu)選評價國內(nèi)外先進凈化工藝的基礎(chǔ)上,確定了適合普光氣田的高含硫天然氣凈化工藝,并首次應用了氣相固定床水解COS、中間胺液冷卻、MAG®液硫脫氣、特大型火炬放空、液硫濕法成型等國際先進工藝和專利技術(shù)。開發(fā)了國內(nèi)首例特大型散裝硫磺料倉、首例5000m3液硫儲罐、首套硫磺流水線轉(zhuǎn)運以及快速定量裝車系統(tǒng),實現(xiàn)200×104t/a硫磺儲運系統(tǒng)的全方位實時監(jiān)控和安全運行。配套開發(fā)先進、靈活、可靠的生產(chǎn)過程控制與安全控制系統(tǒng),確保整個凈化廠處于安全、有效的受控狀態(tài)。高含硫天然氣凈化關(guān)鍵技術(shù)應用于普光氣田后,裝置運行平穩(wěn),產(chǎn)品質(zhì)量合格,各項安全保障到位。為其他大型高酸性氣田的天然氣凈化提供了示范和借鑒。
關(guān)鍵詞:普光氣田;高含硫化氫;天然氣凈化;散裝硫磺;存儲;轉(zhuǎn)運;安全控制;關(guān)鍵技術(shù)
普光氣田是國內(nèi)迄今為止發(fā)現(xiàn)的探明儲量最大、豐度最高的特大型整裝海相氣田,是國家“十一五”重大工程——“川氣東送”建設工程的主供氣源,其硫化氫含量平均達到15%,是目前大規(guī)模開發(fā)的含硫量最高的氣田。普光天然氣凈化廠主要負責高含硫天然氣的凈化以及硫磺儲存運輸,凈化廠建成投產(chǎn)后,年處理天然氣能力為120×108m3,生產(chǎn)硫磺200×104t,綜合排名世界首位。開發(fā)、建設如此規(guī)模的特大型高含硫天然氣凈化裝置以及配套硫磺成型與儲運系統(tǒng),形成完善的天然氣凈化配套技術(shù),并且實現(xiàn)其安全、平穩(wěn)生產(chǎn),國內(nèi)外尚無先例。
針對普光天然氣凈化廠面臨的凈化難度大、產(chǎn)品儲運風險高、異常工況下放空量巨大、安全生產(chǎn)控制交錯復雜等諸多技術(shù)難題,深入開展高含硫天然氣凈化工藝、200×104t/a硫磺安全儲運、大型凈化廠安全運行控制與應急管理等關(guān)鍵技術(shù)的研究與開發(fā),加強新技術(shù)、新工藝、新裝置的引進、消化、吸收與應用,形成了高含硫天然氣凈化、特大型硫磺安全儲運及生產(chǎn)安全控制系列配套技術(shù),實現(xiàn)了特大型高含硫天然氣凈化廠安全、高效、環(huán)保運行。
1 高含硫天然氣凈化工藝技術(shù)
1.1 高含硫天然氣凈化工藝優(yōu)選
普光氣田天然氣富含H2S(15%)和CO2(8%),其有機硫含量也達到340mg/m3以上。天然氣凈化后,要求產(chǎn)品氣質(zhì)量達到《天然氣》(GB 17820—1999)二類氣指標,硫磺質(zhì)量達到《工業(yè)硫磺》(GB/T 2449—2006)一等品指標;同時滿足凈化技術(shù)先進、工藝成熟、操作安全的要求。為此,對WorleyParsons、Black&Veatch、Siirtec Nigi等3家國際知名天然氣凈化技術(shù)專利商的脫硫、脫水、硫磺回收、尾氣處理及酸水汽提5個單元工藝技術(shù)進行綜合評價和優(yōu)選,最終形成適合普光氣田的高含硫天然氣凈化工藝路線(圖1):MDEA法[1]+催化水解脫硫脫碳、TEG法脫水[2]、克勞斯熱轉(zhuǎn)化+二級催化轉(zhuǎn)化法回收硫磺、在線制氫還原吸收+熱焚燒尾氣處理與常規(guī)單塔酸性水汽提[3]。
1.2 高含硫天然氣選擇性脫硫脫碳技術(shù)
1.2.1兩級吸收及級間胺液冷卻工藝
針對原料氣處理量大、H2S與C02含量高,設計兩級吸收塔凈化工藝,應用先進的級間胺液冷卻專利技術(shù)控制C02的吸收,也就是在一級、二級吸收塔之間設置級間冷卻系統(tǒng),從而有效抑制C02的吸收,同時增強H2S的均衡吸收,提高了胺液的脫硫脫碳選擇性。
1.2.2脫硫溶劑的串級吸收、聯(lián)合再生工藝
凈化裝置中脫硫單元和尾氣處理單元均采用MDEA溶液作為吸收溶劑,而尾氣中H2S含量不高。因此將尾氣吸收塔的胺液與脫硫單元二級吸收塔的胺液匯合,送至一級吸收塔串級使用,提高了溶劑循環(huán)效率,胺液總循環(huán)量降低10%。同時全部溶劑由胺液再生塔聯(lián)合再生,較常規(guī)設計減少1套再生系統(tǒng)[4],顯著節(jié)省設備投資與再生能耗。
1.2.3氣相水解脫除有機硫技術(shù)
原料氣中有機硫[5]含量波動范圍大,但主要組成為COS,國內(nèi)首次應用氣相固定床水解COS專利技術(shù),將一級凈化天然氣引入氣相固定床反應器,在低溫催化劑的作用下,COS水解為H2S和C02,進入二級吸收塔脫除。經(jīng)過優(yōu)化操作,COS脫除率可達到99%,產(chǎn)品氣總硫含量(以硫計)小于100mg/m3。與常規(guī)的物理溶劑吸收法邸]相比,氣相水解法未添加新溶劑,無需增設溶劑再生裝置,節(jié)省投資,操作簡單。
1.3 單列20×104t級硫磺回收及在線制氫尾氣處理技術(shù)
1.3.1單列20×104t級硫磺回收技術(shù)
硫磺回收單元采用一段高溫熱轉(zhuǎn)化加兩段低溫催化轉(zhuǎn)化克勞斯下藝[7]。由于單列處理規(guī)模達到20×104t/a,國內(nèi)首次開發(fā)單體20×104t/a克勞斯反應爐,集成高溫熱轉(zhuǎn)化、低溫催化轉(zhuǎn)化、先進的前饋一反饋克勞斯反應控制技術(shù),形成單列20×104t/a特大型改良克勞斯硫磺回收技術(shù),實現(xiàn)兩級催化回收率大于等于95%。
1.3.2液硫深度脫氣技術(shù)
對比國內(nèi)外液硫脫氣工藝后,采用了MAG®液硫脫氣工藝。液硫經(jīng)過循環(huán)流動、冷卻器冷卻、脫氣噴射器機械攪動,使溶解其中的H2S釋放。與常規(guī)的脫氣裝置[8]相比,該工藝不需要額外的化學藥劑和脫氣風機,完全在液硫池內(nèi)完成。經(jīng)過優(yōu)化操作,保證下游硫磺儲運生產(chǎn)安全。
1.3.3在線制氫還原吸收尾氣處理技術(shù)
凈化廠沒有專門的氫氣來源,在尾氣加氫還原吸收工藝[7]中,采用在線加熱爐發(fā)生次氧化反應,提供加氫反應所需的熱源及還原氣體,省去了單獨的制氫裝置。開發(fā)先進的在線加熱爐交叉限幅次氧化燃燒控制技術(shù),精確控制尾氣在線制氫、低溫催化加氫反應,總硫回收率大于等于99.8%,實現(xiàn)了尾氣達標排放。
1.4 75×104m3/h特大型火炬放空技術(shù)
結(jié)合天然氣凈化裝置處理規(guī)模大、聯(lián)合裝置之間影響小的特點,研究東西區(qū)凈化裝置的各種事故放空工況,開發(fā)了凈化裝置“保壓、0.5MPa、1.0MPa”3級放空和凈化廠東西區(qū)區(qū)域放空控制技術(shù),突破常規(guī)12系列裝置全量放空的設計思路,確定火炬系統(tǒng)最大放空量為75×104m3/h,滿足凈化裝置在不同工況下的放空需求。在開停車、聯(lián)鎖關(guān)斷工況下,應用優(yōu)化的高效多點伴燒火炬頭設計和雙保障點火、防空氣倒灌技術(shù),實現(xiàn)普光氣田凈化廠、集氣站、管線等裝置最高75×104m3/h高壓高含硫放卒氣的完全、穩(wěn)定、充分燃燒。
2 200×104t/a硫磺安全儲運技術(shù)
2.1 大型液硫儲罐安全儲存技術(shù)
凈化廠日產(chǎn)液硫能力達7000t,按照國內(nèi)在建的最大罐容2000m3的液硫罐設計,仍需儲罐26個,占地面積過大,相應的場地平整、設備及運行成本也較高。在國內(nèi)首次開發(fā)了單罐容積5000m3的固定式拱頂液硫儲罐,突破液硫溫度徑向梯度限制,以全方位大型液硫儲罐分組溫控技術(shù),解決了存儲溫度不均勻、液硫易凝固、蒸汽耗量大等難題。配套開發(fā)了罐頂固定式蒸汽爆破滅火技術(shù)與大型儲罐內(nèi)壁噴鋁防腐技術(shù),提高儲罐的安全性能,確保10座儲罐、儲存總量5×104m3的特大型液硫罐區(qū)安全、穩(wěn)定運行。
2.2 濕法硫磺成型技術(shù)
由硫磺成型工藝比較(表1)可見,凈化廠若采用單列產(chǎn)能500~1000t/a的硫磺成型工藝,需10余臺硫磺成型裝置,占地面積大,運行及維護成本高。單列產(chǎn)能2000t/d以上工藝相互對比,空冷造粒工藝能耗高,硫磺脆度大,在運輸過程中易形成粉塵,帶來火災、爆炸隱患;而經(jīng)水冷造粒成型的硫磺,硬度大,含水,不易產(chǎn)生粉塵。因此,凈化廠采用國內(nèi)首套濕法硫磺成型工藝,建成4套DEVC0濕法成型機,產(chǎn)能360t/h,硫磺適宜的含水量降低了生產(chǎn)及裝車過程的粉塵,安全性能高。
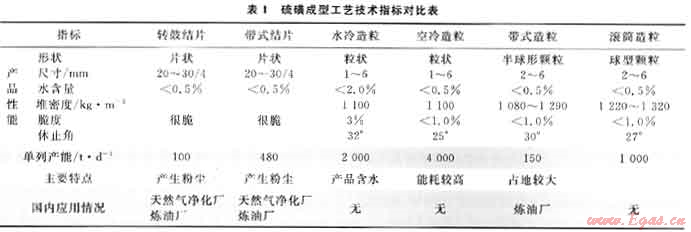
2.3 散裝硫磺料倉安全儲存技術(shù)
針對凈化廠200×104t/a硫磺生產(chǎn)能力,在國內(nèi)首次建設了2座直徑80m、單座容量5.7×104t的特大型圓形料倉,堆料能力為500t/h,取料能力為1000t/h。圓形料倉為半封閉結(jié)構(gòu),環(huán)形擋墻高15m,料場頂部為穹頂網(wǎng)殼鋼結(jié)構(gòu),擋墻和鋼結(jié)構(gòu)表面做防腐和防火處理[9],采用自然通風、機械進風[10]及濕式噴霧粉塵抑制系統(tǒng),有效抑制料倉硫磺粉塵;并配備煙霧、粉塵濃度監(jiān)控系統(tǒng)、硫磺溫度監(jiān)測系統(tǒng)、有毒氣體(H2S)監(jiān)測系統(tǒng)、電視監(jiān)控和火災探測報警系統(tǒng)等安防系統(tǒng),對料倉進行火焰、溫度、粉塵濃度、有毒氣體的全方位實時監(jiān)測與預警;開發(fā)料倉內(nèi)火災報警系統(tǒng)與自動尋的消防炮遠程聯(lián)動技術(shù),配備水霧輔助滅火系統(tǒng),確保消防系統(tǒng)靈活、可靠,提高了硫磺儲存的安全性。
2.4 200×104t/a散裝硫磺轉(zhuǎn)運技術(shù)
硫磺轉(zhuǎn)運系統(tǒng)南大型堆取料機、多條皮帶輸送機、多個轉(zhuǎn)運站、相應的除塵系統(tǒng)、分料系統(tǒng)組成。各轉(zhuǎn)運站設計采用不銹鋼弧形導流抑塵落料管,對料流全程導流,避免了積料、掛料、堵料現(xiàn)象;應用抗雷導靜電技術(shù),將產(chǎn)生的靜電及時導出,設計避雷帶、避雷針,保護除塵設備免受雷擊的侵害。各皮帶機驅(qū)動裝置均采用防爆電機,沿線設置了拉繩開關(guān)、跑偏開關(guān)、速度檢測開關(guān)等保護裝置,集成轉(zhuǎn)運系統(tǒng)聯(lián)鎖、皮帶跑偏控制、皮帶速度檢測、溫度和粉塵檢測、料流堵塞檢測技術(shù),實現(xiàn)200×104t/a硫磺轉(zhuǎn)運系統(tǒng)的自動化流水線轉(zhuǎn)運、無人值守、無害化作業(yè)。
2.5 快速定量裝車技術(shù)
裝車系統(tǒng)由2座高30m的裝車樓及相應的快速定量裝車系統(tǒng)組成??焖俣垦b車樓是基于大型料斗秤,預先在定量倉中按集裝箱標重裝載,通過閘門和卸料溜槽控制,向行進中的集裝箱快速卸料,實現(xiàn)一次性連續(xù)動態(tài)快速準確裝車,裝車能力650t/h,單個集裝箱裝車稱重誤差低于0.1%。
快速定量裝車系統(tǒng)應用液壓控制、定量稱重與機車自動定位技術(shù),集成伸縮式料管裝車、噴霧抑塵與粉塵回收系統(tǒng),實現(xiàn)硫磺定量自動密閉裝車,減少了粉塵飛揚,提高了裝車安全性。
3 安全運行控制與應急管理技術(shù)
3.1 大型裝置生產(chǎn)運行控制技術(shù)
由于凈化裝置工藝技術(shù)運行條件苛刻、測控點多、控制復雜,為確保裝置安全、長周期、平穩(wěn)運行,采用分散控制系統(tǒng)(DCS),對工藝過程進行集中控制、檢測記錄和報警。建立了區(qū)域獨立控制與中控集中控制相結(jié)合的DCS系統(tǒng)構(gòu)架,開發(fā)分類組織的上位組態(tài)模式,集成1Gbps超大帶寬冗余總線控制技術(shù),實現(xiàn)凈化廠20000個控制點大規(guī)模生產(chǎn)指令數(shù)據(jù)的實時、快速交換與通訊,確保系統(tǒng)安全、靈敏、可靠,年穩(wěn)定運行大于等于8400h,控制反應時間小于等于200ms、準確率為100%。
3.2 安全聯(lián)鎖控制技術(shù)
從凈化廠生產(chǎn)過程控制、危險源、風險評估、應急預案等實際出發(fā),研究凈化廠設備、單元、聯(lián)合裝置以及全廠東、西區(qū)域在正常生產(chǎn)過程中的彼此關(guān)聯(lián)因素,設計氣田上下游一體化緊急關(guān)斷,科學劃分聯(lián)鎖區(qū)域,設計保壓、0.5MPa/min放空、1.0MPa/min放空3種分級關(guān)斷模式,采用雙“二選一”結(jié)構(gòu),形成安全等級高、兼容性強的四級聯(lián)鎖關(guān)斷技術(shù)。
中心控制室設置1套SIS系統(tǒng),實現(xiàn)一、二級關(guān)斷;每套聯(lián)合裝置4套SIS系統(tǒng)實現(xiàn)三、四級關(guān)斷;從而實現(xiàn)全廠、區(qū)域與各聯(lián)合裝置獨立關(guān)斷,在有效保證安全的情況下降低了環(huán)境的污染。
3.3 安全防護與應急管理技術(shù)
凈化廠工藝設施中危險源、工藝失效事件種類多,工藝裝置泄漏頻率偏高,導致凈化廠安全生產(chǎn)風險偏大,增加潛在的安全隱患。鑒于國內(nèi)未形成完善的量化風險評價標準和規(guī)范,采用國際先進的Safety、Leak等系統(tǒng)對普光凈化廠整體進行國內(nèi)首次安全量化風險評價(QRA)。依據(jù)量化風險評價結(jié)果,指導全廠硫化氫、可燃氣體泄漏監(jiān)測、火災報警、視頻監(jiān)控、安全逃生、應急疏散等安全控保系統(tǒng)科學設計、合理布局,建立了完善的安全管理與應急預案體系,實現(xiàn)凈化廠的全方位實時監(jiān)控及異常情況下的有效處置,將風險的整體等級降到最低合理可行的范圍。
4 關(guān)鍵技術(shù)的應用效果
特大型高含硫天然氣凈化及配套技術(shù)在普光氣田得到成功的應用。從2009年10月普光天然氣凈化廠第一聯(lián)合裝置順利試投產(chǎn)以來,目前6套聯(lián)合裝置均已開車成功,凈化裝置運行平穩(wěn),主要工藝技術(shù)指標達到設計要求,凈化產(chǎn)品氣達到《天然氣》(GB 17820—1999)二類氣標準,硫磺質(zhì)量達到《工業(yè)硫磺》(GB/T 2449—2006)一等品質(zhì)量指標,實現(xiàn)環(huán)保生產(chǎn)。液硫罐區(qū)、硫磺成型、硫磺倉儲、轉(zhuǎn)運以及定量裝車設施安全有序運行,生產(chǎn)控制與聯(lián)鎖關(guān)斷系統(tǒng)穩(wěn)定可靠,指令響應迅速,關(guān)斷控制準確,全廠處于安全平穩(wěn)運行狀態(tài),經(jīng)濟效益顯著。
5 結(jié)論
普光氣田天然氣凈化廠各聯(lián)合裝置、硫磺儲運系統(tǒng)順利投產(chǎn)后,產(chǎn)品指標合格、裝置運行平穩(wěn),以實踐證明了天然氣凈化廠關(guān)鍵技術(shù)應用的可靠性,為今后我國高酸性氣田大型天然氣凈化廠的開發(fā)、設計和建造提供了寶貴的經(jīng)驗和良好的借鑒。
1) MDEA法+催化水解脫硫脫碳、TEG法脫水、克勞斯熱轉(zhuǎn)化+二級催化轉(zhuǎn)化法回收硫磺、在線制氫還原吸收+熱焚燒尾氣處理與單塔酸性水汽提工藝,滿足普光氣田大規(guī)模高含硫天然氣凈化的要求,產(chǎn)品質(zhì)量合格,尾氣排放達標。
2) 硫磺大型機械化倉儲、流水線轉(zhuǎn)運、自動快速定量裝車、鐵路集裝箱外運技術(shù)首次有機整合應用于硫磺儲運系統(tǒng),形成的200×104t/a硫磺安全儲存技術(shù),能夠?qū)崿F(xiàn)超大規(guī)模硫磺儲運系統(tǒng)的全方位實時監(jiān)控和安全運行。
3) 開發(fā)的大型凈化廠安全運行控制與應急管理技術(shù),生產(chǎn)控制與聯(lián)鎖關(guān)斷系統(tǒng)穩(wěn)定可靠,指令響應迅速,關(guān)斷控制準確,滿足凈化廠安全生產(chǎn)控制要求。
參考文獻
[1] 王開岳,徐德明.四川天然氣凈化及硫磺回收工藝技術(shù)近況[J].硫酸工業(yè),1990(3):34-38.
[2] 張良,劉勇,韓超.三甘醇脫水裝置影響因素定量分析[J].內(nèi)蒙古石油化工,2010,36(8):24-27.
[3] 劉玉峰,王春梅,生旺泉.酸性水汽提與硫磺回收裝置的處理工藝[J].石油和化工設備,2009,12(12):51-54.
[4] 符秀蘭.脫硫溶劑MDEA的再生工藝[J].硫磷設計與粉體工程,2007(4):30-33.
[5] 溫崇榮,馬利,常宏崗.川東北高含硫天然氣脫硫凈化技術(shù)研究[D].重慶:重慶大學,2000.
[6] 章建華,沈本賢,劉紀昌,等.高酸性天然氣中有機硫在溶劑吸收中的選擇性研究[J].石油與天然氣化工,2009,38(3):203-206.
[7] 王開岳.天然氣凈化工藝:脫硫脫碳、脫水、硫磺回收及尾氣處理[M].北京:石油工業(yè)出版社,2005.
[8] 吳煒.液硫脫氣裝置:中國,200520035063.7[P].2006-09-06.
[9] 劉焰.硫磺倉庫防火設計分析[J].硫磷設計與粉體工程,2003(4):4-6.
[10] 桂偉東.從兩起硫磺燃燒事故探討防火防爆安全措施[J].化工安全與環(huán)境,2003(28):11-14.
(本文作者:于艷秋 毛紅艷 裴愛霞 中國石化中原油田普光分公司天然氣凈化廠)
贊 賞 分享
您可以選擇一種方式贊助本站
支付寶轉(zhuǎn)賬贊助
微信轉(zhuǎn)賬贊助
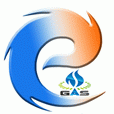
- 注解:本資料由會員及群友提供僅供閱讀交流學習,不得用于商業(yè)用途!